Overview
SOP provides system settings that can be customized to align with company workflow and policies. Administrators have access to the system settings through the drop-down menu in the top right corner of the interface.
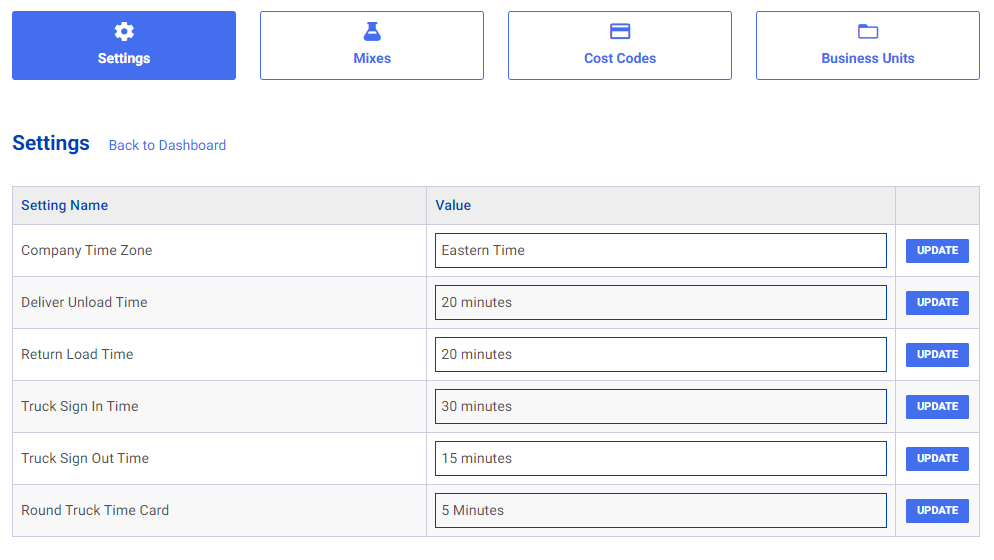
Default Start Adjustment Time
This setting configures the number of minutes to start a truck’s work shift before their first load. For example, if a truck is first loaded at 8:00 AM for a job shift and the default start adjustment time is set to 15 minutes, that truck’s sign in time will automatically default to 7:45 AM.
Default start adjustment can be changed for individual jobs, overriding the default start adjustment for that shift. Individual truck sign in times can also be adjusted from the truck time report or plant manager’s dashboard.
If set to 0, no time will be added to the sign in time.
Default Delivery/Return Adjustment Times
SOP uses dynamic traffic routing to determine the travel time between truck loading and unloading locations. The default delivery and return adjustments add a set number of minutes to the travel time to allow for expected delays at each location.
For example, if a truck is loaded at 8:00 AM, the travel time is 45 minutes, and the default start adjustment is set to 15 minutes, the truck’s ETA to the unload location will be 9:00 AM. Travel progress bars will show elapsed time based on 60 minutes.
The default delivery and return adjustments can be changed for individual jobs, overriding the default configuration for all loads added to that job.
If set to 0, no time will be added to the routing.
Truck Sign Out Time Settings
SOP allows you to set a default truck sign-out time, based on the job shift’s return travel time. The settings include a percentage of the return time, a fixed number of minutes, and a maximum time. These settings can be used in combination to customize how many minutes to add to a truck time card after it is unloaded for the last time.
For instance, you may want to pay a driver 50% of the return time, plus 15 minutes for cleanout. You may also want to limit the time to 1 hour total in the case of longer trips.
Scheduled Start Alert Threshold
Use this setting to highlight truck start times on the time report when they exceed a certain number of minutes. For instance, if a truck isn’t loaded for 40 minutes after its scheduled start time, and this setting is set to 30 minutes, the 40-minute start time will be highlighted in red.
Mixes
SOP automatically generates new mix design names from the scale system. Administrators can manage mix designs by using the Mixes button in the System Settings area. This allows the addition of new mix designs or modification of existing ones.
Note: Editing an existing mix design will change any job shifts with this mix design.
Cost Codes
New Cost codes are automatically created in SOP from the scale system. Use the Cost Codes button at the top to manage your Cost Codes or Phases in SOP. You can add new Cost Codes for scheduling or edit an existing Cost Code.
Note: Editing an existing cost code will change any job shifts or loads with this cost code.
Business Units
Contractors can set up business units in SOP to group jobs for user views and reporting purposes. Once configured, users can filter jobs on the dashboard based on business units. They also have the option to set their default business unit in their profile, which automatically filters their job list accordingly.
Business units are assigned to new jobs based on the first character of the job number. If your organization follows a different method for assigning jobs, contact [email protected]. Jobs can also be edited to manually assign a business unit.